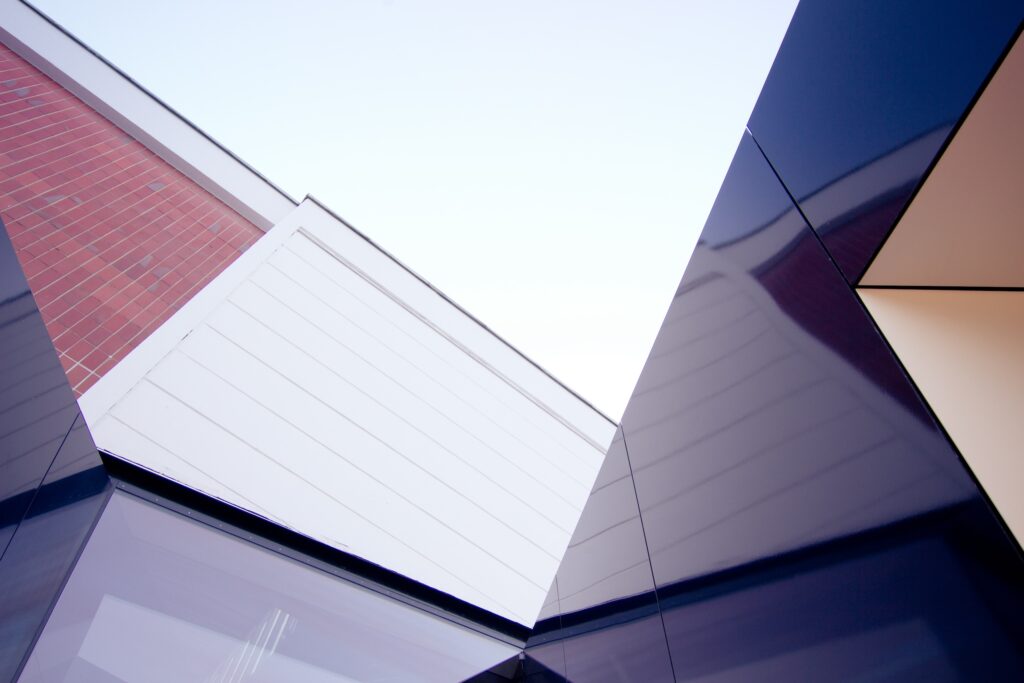
QM certification
for medical devices
Certification according to QM standards in industry, trade and services
According the standards
EN ISO 9001
EN ISO 13485
QM CERTIFICATION
A well-considered and practised quality management system offers confidence in daily actions and activities and thus represents a stable principle of corporate caution.
The aim of quality management is to ensure and continuously improvement of performance and quality development of a company/organisation. Implemented accordingly, a QM system brings many advantages, such as increased product and service reliability and thus the expansion of a company’s own competitive position. Optimised processes and thus increasing effectiveness and efficiency are combined with the improvement of quality in the company. Properly understood and implemented, it represents a guideline for effective corporate management that takes current legal requirements (which cannot be ignored) into account.
Certification according to QM standards is an added value for all protagonists in the medical device environment. Regardless of whether you are a service provider, distributor, manufacturer (series and customised production) or contract manufacturer – you will receive an objective assessment of your QM system and the underlying company processes.
The QM certifications we offer cover different QM standards. In addition to the industry-specific EN ISO 13485 standard, we also offer certification in accordance with the universally applicable EN ISO 9001 standard.
By combining audits within the framework of CE and QM certification, we can also optimize the use of resources.
Contact
Contact us for more information on QM certification
EN ISO 13485
Here you can find further information on product EN ISO 13485
EN ISO 9001
Here you can find further information on product EN ISO 9001
Requirements for quality management
The aim of a quality management system is to ensure and continuously improve process and product quality in companies. The standard provides a framework with subject areas for the implementation of this:
a) Handling documents and records
- How do I manage information (internally and externally)?
- How do I avoid document chaos?
- How do I find my records again?
- Which regulatory requirements need to be taken into account?
b) Management tasks
- How do I regulate responsibilities and authorisations in my company?
- Who is authorised to do what and why?
- How do I implement the QM system in practice?
- What tools do I have at my disposal?
c) Dealing with operational resources
- What equipment and infrastructure do I need?
- What personnel expenditure is necessary?
- Which training and further education programmes are required and how effective are they?
d) Core process(es):
- How do I plan the processes?
- What (supply / product / process) risks do I need to take into account?
- What are the customer requirements (patient, payer…)?
- How do I implement these appropriately?
- How do I manage the procurement of the necessary resources and any external services?
- How do I manage my (value-adding) processes?
- Are there processes that cannot be measured by their results?
- How are these to be validated and thus safeguarded in the result?
e) Review:
- How do I check my processes and their results?
- What information, data and tools do I use for this?
- Have any reportable incidents been identified – is communication with the authorities necessary?
- What do my customers say?
- What conclusions do I draw from the above information and
Do you have any questions?
We will answer your questions as soon as possible.
THERE IS NOTHING LIKE PERSONAL CONTACT
FAQ
What is a quality management system?
A quality management system (QMS) is a systematic and organised set of processes, procedures and responsibilities that an organisation uses to improve and control its products, services and processes in compliance with standards. The aim of a QMS is to ensure and improve the quality of results, increase customer satisfaction and reduce costs. In order to be able to react to changing market and customer requirements, a QMS must be constantly adapted and is therefore referred to as a “living system”.
Upcoming events
EVENTS BY MDC
Open vacancies
CAREER AT MDC